Choosing the right facilities and equipment maintenance plan is difficult, but vital. How can you balance the upfront and overall costs while taking care of the health and safety of both your facility and people? What maintenance plan is best? Here are three basic types of maintenance plans to consider:
Preventative Maintenance is a type of proactive maintenance and is performed on a scheduled basis at timed intervals. Following a maintenance schedule will extend the life of the equipment and keep its performance level at peak capacity as the designers/engineers originally intended.
Pros: This plan is cost effective and increases equipment life cycle and energy savings.
Cons: It is labor intensive and may include some unnecessary maintenance at times.
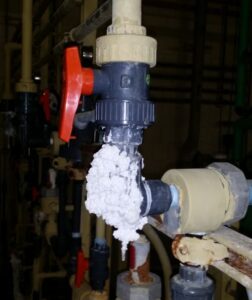
Predictive Maintenance is another type of proactive maintenance and is performed based on the condition of the machine or equipment rather than at timed intervals. This plan requires scheduled testing rather than scheduled maintenance of machinery and equipment. Maintenance is performed as the scheduled testing and test results dictate.
Pros: This plan, when implemented correctly, can decrease downtime, avoid unnecessary maintenance, decrease cost of labor and materials, and save energy.
Cons: It requires rigorous planning, staff training and diagnostic equipment to see the potential savings.
Deferred Maintenance is reactive maintenance and is performed only after something breaks down. There is little to no maintenance done to ensure the longevity and peak performance of the equipment until this point. This plan is common and, unfortunately, the most detrimental of the three plans.
Pros: This plan allows for lower upfront costs and staffing.
Cons: It leaves the facility vulnerable to unplanned outages, increased overall repair costs, and injuries. In addition, it will often void any manufacturer warranties by not providing the appropriate maintenance.
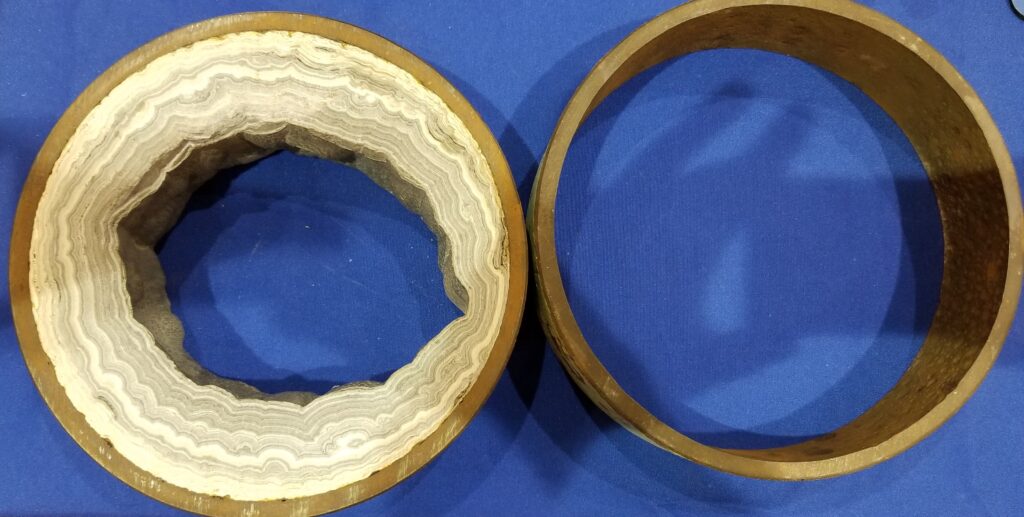
Each maintenance plan has its own advantages and disadvantages, however, beware of the deferred reactive maintenance plan. As one of our customers recently told me, “Deferred maintenance is a poisoned procedure.” It is often practiced by default, so double-check that you are not susceptible to these 8 dangers of deferred maintenance:
1.
Emergencies Cost More. When you have an emergency repair, the cost of materials, expedited freight, emergency labor, and downtime add up quickly. Emergency shutdowns often happen during peak operation periods, making the repairs more expensive and often more scrutinized. Avoid these costs by having planned, scheduled maintenance.
2.
Public View. Perception of whole industries can be jaded from a catastrophic accident or injury. If public view of an industry is negative it may be difficult to obtain future funding within the sector.
3.
Forced Outages. There’s no good time for a forced outage. Outages should be done on your terms, when it’s best for your staffing, budget, and capacity needs. Unscheduled maintenance from a forced emergency outage leaves you scrambling to find appropriate craft, procure materials, and obtain any required permits while also suffering loss in production and revenue.
4.
Health and Safety Risk to Employees. Any process, facility, or equipment can become dangerous to the health and safety of employees and visitors if regular maintenance does not occur. Injuries due to deferred maintenance can increase insurance costs and legal fees while decreasing morale and productivity. Scheduled testing by facility professionals who can recognize and recommend needed maintenance will keep your facility running in tip-top shape while keeping occupants safe.
5.
Shortened Life Cycle. We all know that if we do not take care of things, they won’t take care of us. Why would your facility and equipment be any different?
6.
Reduced Efficiencies. Equipment that is not regularly maintained will use more energy, lowering its overall performance. Reduced efficiencies can lead to the loss of LEED points and Green rating.
7.
Long-Term Cost. More than likely, the lowest cost available for parts or replacement is now as prices typically increase annually. Each year the cost may only go up fractionally, but deferring maintenance 5-10 years can ultimately add up to a significantly higher price tag.
8.
Back-Log. Once deferred maintenance starts it can quickly escalate into an overwhelming backlog that you may not be able to manage or overcome without a major plant/equipment overhaul or replacement.
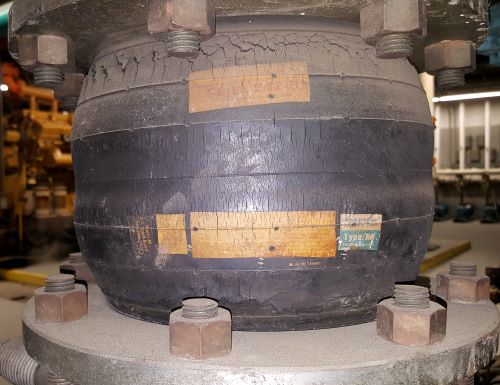
Spend money now or spending more money later is an on-going balancing act. As a maintenance professional you can elevate your game by –
- Understanding the rapid escalation of costs.
- Showing how your proactive plan minimizes your facility’s rate of decay and mitigates costs into a manageable budget.
- Obtaining adequate funding for your plan and documenting its effectiveness.
If you would like support in creating or revitalizing your plant’s proactive Maintenance Plan regarding piping systems (including expansion joints and valves) we are happy to perform a walk-through to help you stay on track.
Choosing the right facilities and equipment maintenance plan is difficult, but vital. How can you balance the upfront and overall costs while taking care of the health and safety of both your facility and people? What maintenance plan is best? Here are three basic types of maintenance plans to consider:
Preventative Maintenance is a type of proactive maintenance and is performed on a scheduled basis at timed intervals. Following a maintenance schedule will extend the life of the equipment and keep its performance level at peak capacity as the designers/engineers originally intended.
Pros: This plan is cost effective and increases equipment life cycle and energy savings.
Cons: It is labor intensive and may include some unnecessary maintenance at times.
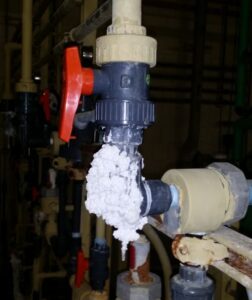
Predictive Maintenance is another type of proactive maintenance and is performed based on the condition of the machine or equipment rather than at timed intervals. This plan requires scheduled testing rather than scheduled maintenance of machinery and equipment. Maintenance is performed as the scheduled testing and test results dictate.
Pros: This plan, when implemented correctly, can decrease downtime, avoid unnecessary maintenance, decrease cost of labor and materials, and save energy.
Cons: It requires rigorous planning, staff training and diagnostic equipment to see the potential savings.
Deferred Maintenance is reactive maintenance and is performed only after something breaks down. There is little to no maintenance done to ensure the longevity and peak performance of the equipment until this point. This plan is common and, unfortunately, the most detrimental of the three plans.
Pros: This plan allows for lower upfront costs and staffing.
Cons: It leaves the facility vulnerable to unplanned outages, increased overall repair costs, and injuries. In addition, it will often void any manufacturer warranties by not providing the appropriate maintenance.
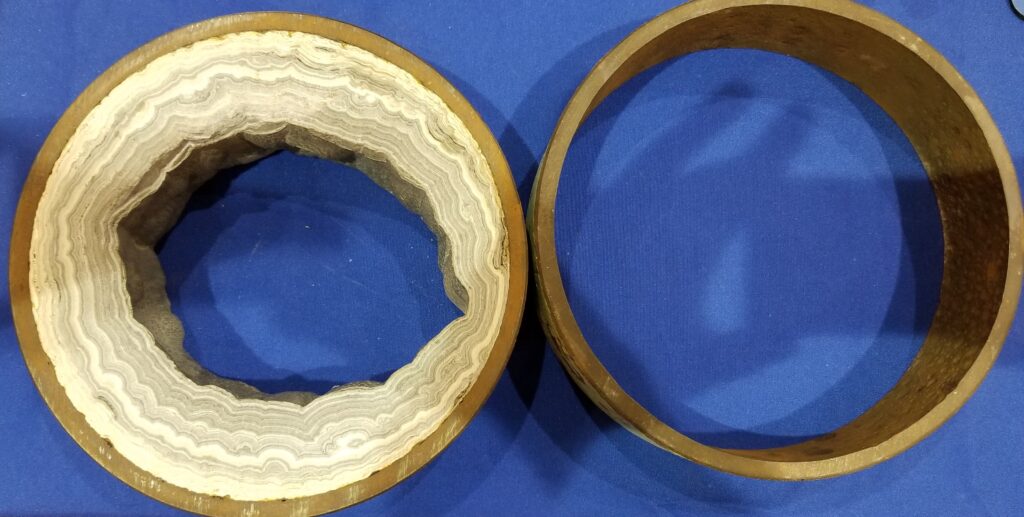
Each maintenance plan has its own advantages and disadvantages, however, beware of the deferred reactive maintenance plan. As one of our customers recently told me, “Deferred maintenance is a poisoned procedure.” It is often practiced by default, so double-check that you are not susceptible to these 8 dangers of deferred maintenance:
1. Emergencies Cost More. When you have an emergency repair, the cost of materials, expedited freight, emergency labor, and downtime add up quickly. Emergency shutdowns often happen during peak operation periods, making the repairs more expensive and often more scrutinized. Avoid these costs by having planned, scheduled maintenance.
2. Public View. Perception of whole industries can be jaded from a catastrophic accident or injury. If public view of an industry is negative it may be difficult to obtain future funding within the sector.
3. Forced Outages. There’s no good time for a forced outage. Outages should be done on your terms, when it’s best for your staffing, budget, and capacity needs. Unscheduled maintenance from a forced emergency outage leaves you scrambling to find appropriate craft, procure materials, and obtain any required permits while also suffering loss in production and revenue.
4. Health and Safety Risk to Employees. Any process, facility, or equipment can become dangerous to the health and safety of employees and visitors if regular maintenance does not occur. Injuries due to deferred maintenance can increase insurance costs and legal fees while decreasing morale and productivity. Scheduled testing by facility professionals who can recognize and recommend needed maintenance will keep your facility running in tip-top shape while keeping occupants safe.
5. Shortened Life Cycle. We all know that if we do not take care of things, they won’t take care of us. Why would your facility and equipment be any different?
6. Reduced Efficiencies. Equipment that is not regularly maintained will use more energy, lowering its overall performance. Reduced efficiencies can lead to the loss of LEED points and Green rating.
7. Long-Term Cost. More than likely, the lowest cost available for parts or replacement is now as prices typically increase annually. Each year the cost may only go up fractionally, but deferring maintenance 5-10 years can ultimately add up to a significantly higher price tag.
8. Back-Log. Once deferred maintenance starts it can quickly escalate into an overwhelming backlog that you may not be able to manage or overcome without a major plant/equipment overhaul or replacement.
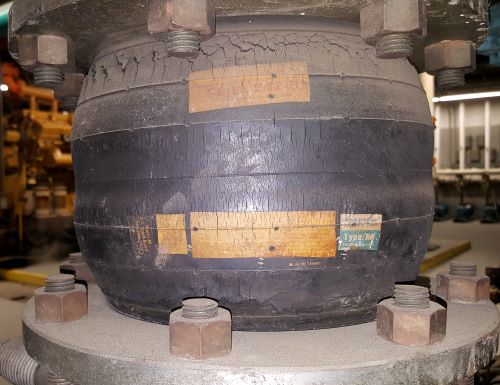
Spend money now or spending more money later is an on-going balancing act. As a maintenance professional you can elevate your game by –
· Understanding the rapid escalation of costs.
· Showing how your proactive plan minimizes your facility’s rate of decay and mitigates costs into a manageable budget.
· Obtaining adequate funding for your plan and documenting its effectiveness.
If you would like support in creating or revitalizing your plant’s proactive Maintenance Plan regarding piping systems (including expansion joints and valves) we are happy to perform a walk-through to help you stay on track.